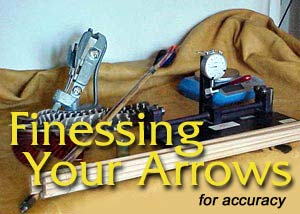
By Larry Yien
This article is meant to supplement
your basic arrow making instructions. Spending a little extra
time on your arrows can reward you with a well-matched set. I
have come up with some tips on arrow making that have brought
my arrows right where I want them to be, in the spot!
I have acquired a handful of tools that
make this fine-tuning possible. After reading the article you
can decide what you need in order to add some finesse to your
arrows.
Electronic grain
scale
Spine tester
Arrow straightener
Gasket lacquer kit
Nock repair tool
Bjorn nock alignment jig
Arrow cutoff tool handsaw
Power taper tool
Order in larger quantities
I like to order my arrows a couple dozen
at a time from an outfit that matches arrows within 5# of spine
weight and 10 grains of mass weight. It allows me to shoot the
same set of arrows longer. If I bust a few arrows I dont
have to make another dozen that may be different. I just reach
into the arrow bin and grab another handful of arrows from the
same set. The extra money you spend to have your dealer match
your arrows is well worth it. It can eliminate the need to spine
and weigh your arrows altogether, although I still like to measure
my shafts regardless.
Prep shafts out of the box
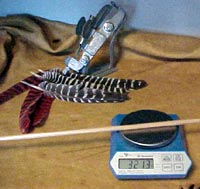
Once that much awaited box of shafts gets
to my doorstep, I take them out of the box and weigh them with
a grain scale to get their weight, and write it on the shaft.
I also verify that the spine weights are close.
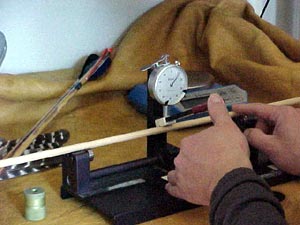
After I weigh them I straighten them with
an arrow straightener, one of those dial indicator straighteners.
Other techniques work well for straightening; I prefer the dial
indicator because it tells me what the shaft is doing quantitatively.
The disadvantage is that they dent the surface of the shaft and
are expensive to purchase. If you find one end of the shaft is
straighter than the other, mark it and use it for the nock end
of the arrow.
This is a good time to apply water base
aniline dyes to the shaft with a brush or rag. I do not stain
my competition arrows, but I do stain my hunting arrows to break
up the lines of the shaft. When I dissolve the aniline dye in
water I make sure the water is hot. After I use the stain I let
the shaft dry overnight and rub down the raised grain with steel
wool.
Gasket lacquer dip
I wipe the any dust off with a clean rag
and dip the shafts. I hold on to the nock end of the shaft and
dip the shafts once. After I dip them all, I start with the first
shaft and dip them again. After the second dip, I flip the shaft
around and hold onto the point end and dip the shafts a third
time. I wipe the nock end off with a rag right after I dip it
to eliminate any build up of gasket lacquer.
I re-weigh the shafts and any shafts that
come out more than 5 grains light - I redip them to add more
weight. A full dip from tip end to nock end is about 10 grains
for a 28 arrow.
I check for straightness with the arrow
straightener at this point.
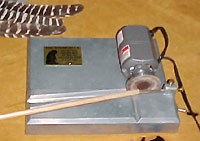
Finally, I crest the shafts, once dry I
cover the crest with clear water base poly as a protective coat.
The crest is more durable with a clear coat over it. I
use a hand cut off saw to get my arrows to a consistent length.
I taper the ends at this stage with a power taper tool, and glue
on the points with hot melt. I prefer the power taper tool because
it gives me an even, and true taper on the nock end as well as
the point end.
Arrow assembly
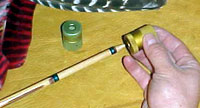
I use a nock repair tool to lightly remove
any excess lacquer off the nock taper. Do not remove all the
lacquer off the taper, just run the tool over the taper to remove
any high spots. Once the tool leaves score lines evenly it is
time to apply the nocks. This taper repair tool is designed for
use on aluminum shafts. Use a small drop of duco cement on the
taper and rotate the nock on. Check the nock for alignment. I
use a Bjorn nock alignment jig. Nock alignment and arrow straightness
in the back 1/3 of the arrow is critical for my arrows.
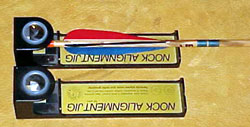
I apply the fletch with duco and place the
back of the fletch 1 inch from the throat of the nock.
Final weigh in
After I assemble the arrows I do a final
weighing of the complete arrow and write the weight on the shaft
near the fletch. This gives me a quick reference when I need
to know the weight. I arrange my arrows from lightest to heaviest
and number them 1-24. This will act as a guide to which arrows
are nearest each other in weight. With numbered shafts you can
also identify arrows that miss the mark and more importantly,
arrows that consistently hit the mark
Enjoy your arrows.
Larry